Turnkey Solution
EWAC Alloys Limited, demonstrating expertise and technical competence in welding and allied products since 1962, has been ceaselessly serving the Maintenance and Repair needs across industries. A pioneer in the Maintenance and Repair field, EWAC’s approach has always been to introduce innovative technologies and fight the WAR against WEAR. The Services business provides Turnkey Solutions to customers, that result in:
- Reduced Downtime
- Enhanced Performance
EWAC leverages its technical skills honed over time through its illustrious heritage of over 60 years.
Services Business Snapshot
EWAC introduced the concept of “Total Turn-Key Solutions” in the Indian market. Our dedicated, pan-India team of highly skilled and experienced engineers offers one-stop repair solutions for Repair & Maintenance welding activities across all process industries, including:
• Cement • Steel • Power • Sugar • Automotive • Engineering
In partnership with our customers and according to their specifications, EWAC provides a comprehensive range of services, customised according to their working conditions. EWAC has a dedicated team of workshop and on-site Services Professionals that adhere to a stringent quality control policy consistently practiced across its network of repair workshops in the country. We have earned the trust and confidence of customers in providing immediate on-site interventions and localised services, thereby saving Equipment Downtime, Inventory Costs, Minimising Lead times, and maximising customer profitability.
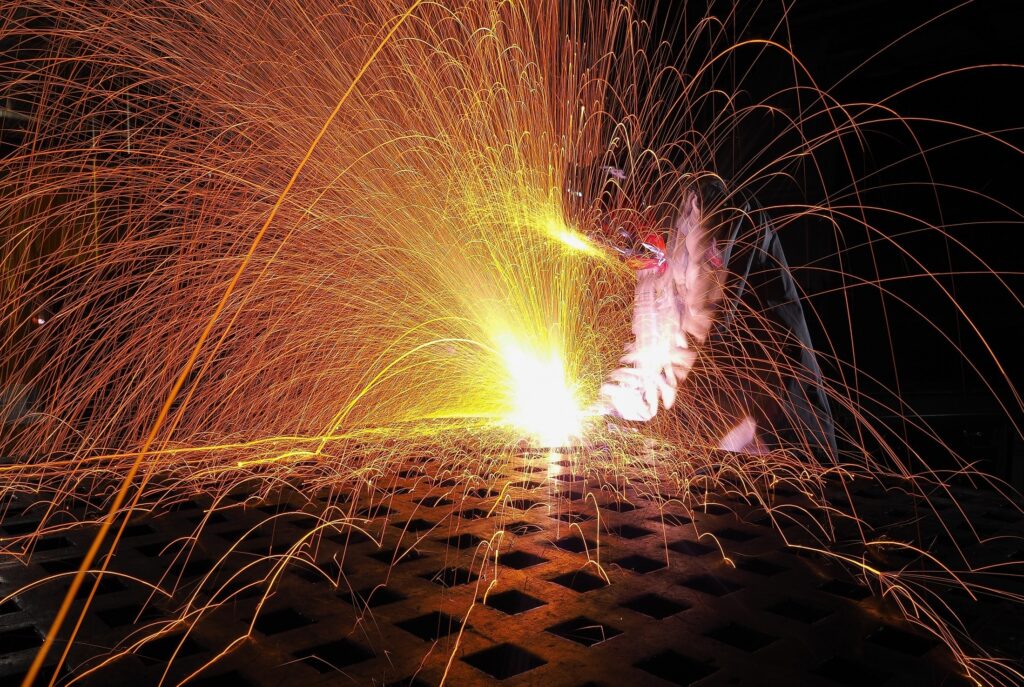
Refurbishment of the Mechanical Component in Steel, Cement, Power, Oil & Gas, Construction etc.
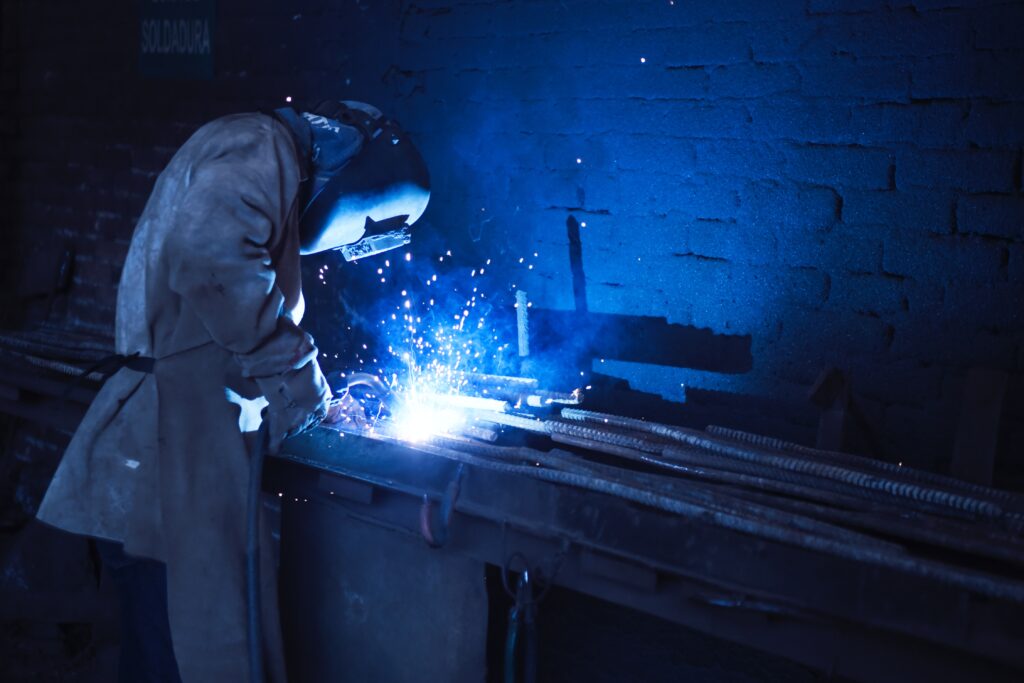
Thermal Spray and HVOF Coating Services
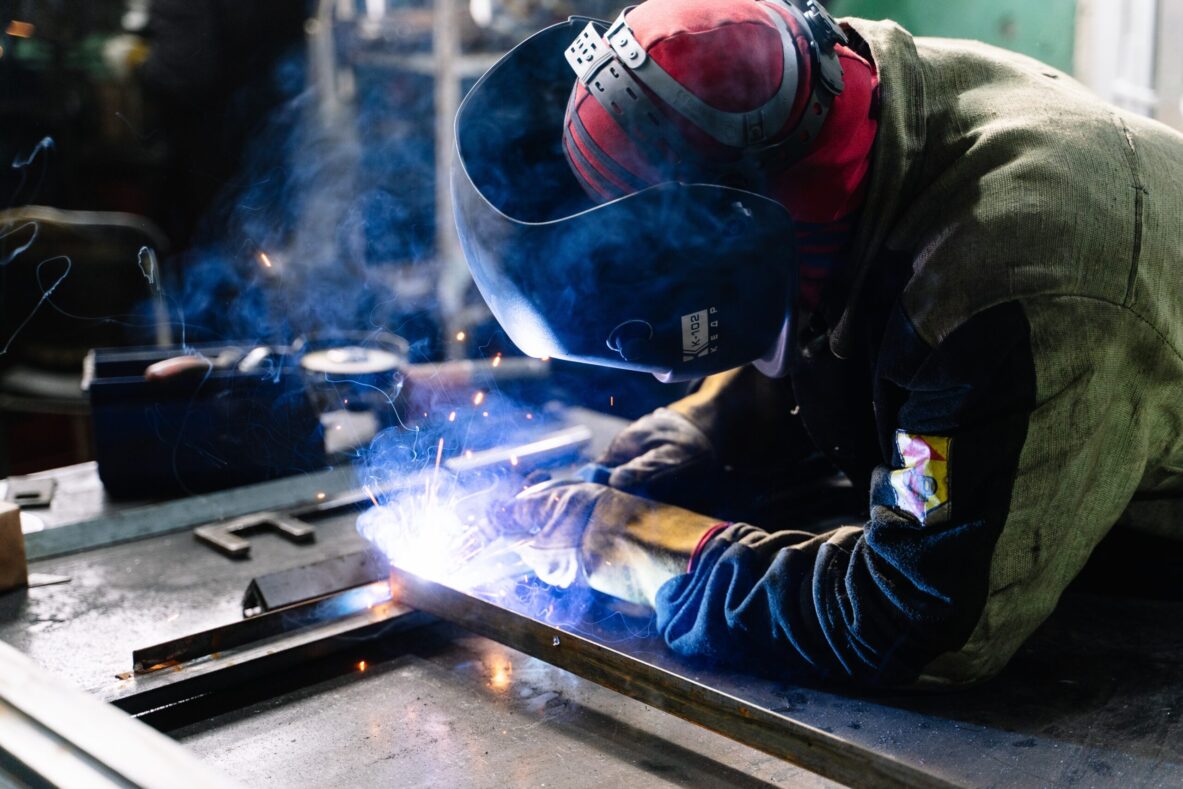
Product development with Value added services
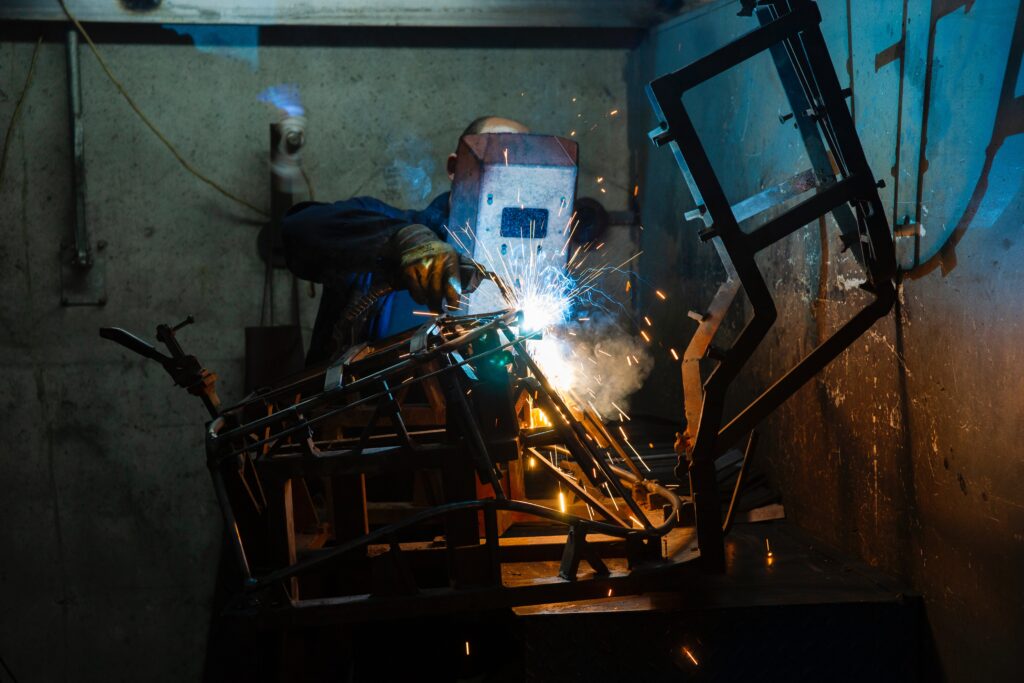
Onsite Welding and Machining services
Sinter Breaker & Grizzly Bars
In an integrated steel plant, the Sinter Plant produces agglomerated mass known as Sinter from iron ore, coke, and flux fines.
After the sintering process, the Single Roll Crusher or the Sinter Breaker is the equipment that crushes large blocks of red hot sinter cakes at 650-900°C, falling from the Pellet Car. The Sinter Breakers consist of 9 to 18 sprockets having 3 or 4 integral radial arms mounted and assembled on a shaft to form a roll crusher. The crusher arms pass between the series of similar numbers of grizzly/grate/knife bars while breaking the sinter cake into smaller sized sinter lumps.
The arms of the Sinter Breaker and the top surface of the Grizzly Bars are subjected to severe impact and abrasion at very high temperatures. So, these two components are subjected to the most rapid wear. Enhancement of their wear life is a task of continuous development for tribologists. Our plethora of customised products and turnkey reclamation technology has successfully established one of the best performances of Sinter Breakers and Grizzly Bars in many integrated steel plants of various capacities. Today, we are a leading supplier of new sets of Sinter Breakers and Grizzly Bars, complete with value-added life-enhancing wear-resistant cladding.
Hammers
In an integrated steel plant big boulders of various minerals like coal, limestone and dolomite are crushed into smaller lumps of uniform size for use, with various types of hammers.
So, we see various hammer mills using hammers of different base materials, shapes and sizes engaged in crushing the above raw materials.
The hammers are subjected to severe impact and abrasion which are replaced at frequent intervals as consumables. EWAC Alloys with its six decades of experience in reclamation technology has developed high performance ready to use crusher hammers for coal and flux. We are a leading supplier of these hammers, are established in many integrated steel plants for their life-prolonging factor, high crushing efficiency, reduced downtime and overall techno economics.
-
- Reducing downtime
- Improvising efficiency
- Reducing Vibrations
- Reducing Energy Consumption
-
-
- Cage/Separator Rotor
- Guide Vanes
- Static Blades/Louvres
- Fans
- Body Liners
- Nozzle Ring Segments
- Yoke
- Cone
- Roller Guard
- Chutes
- Ducts
- Hoppers
- Rotary Airlock
-
-
-
-
- Crushing (primary reduction)
- Grinding (fine reduction)
-
-
-
- Double toggle jaw crushers
- Cone/gyratory crushers
- Roll/hammer crushers
- Ring granulators
- Hammer mills
- Impact crushers
-
-
- Wobblers
- LS Crusher Rotor
- Impactor Arm
- Blow Bar
- Discharge Chute
- Body liners
- Grinding Paths, etc.
-
-
-
- The milled and blended raw materials from mills go to a silo and then to the kiln through the preheater.
- The preheater-kiln system consists of a multi-stage cyclone, rotary kiln, and grate cooler.
- The kiln feed is preheated by hot gas from the combustion chamber and rotary kiln.
- Clinker formation takes place inside a rotary kiln which gets cooled inside the grate cooler.
- In the entire process, the components have to withstand high temperatures up to 1450°C.
-
-
-
- Tongue plates
- Inlet Sector
- Tip Casting
- Grate Plates
- Grizzly bar
- Clinker breaker hammer
- Discharge chutes
- HRB Rolls
- Fans, etc.
-
-
-
- Supply of air or removal of exhaust gases
- Material handling
-
-
-
- Raw Mill Fans
- Preheater Fans
- Induced Draft Fans
- Cooling ID Fans
- Raw Mill Exhaust Fans
- Coal Mill Fans
- Cooler Exhaust Fans
-
-
- Extend the fan service life
- Save Energy
- Reduce other components’ maintenance costs
Coal Burner Nozzle & Tip
The Coal Burner Nozzle and Tip Assembly inject pulverised coal through the splitter plates tangentially from the four corners of a boiler. The three main factors determining the efficiency of the coal burner nozzle and tip are the flue-gas exit temperature, excess air, and burnout.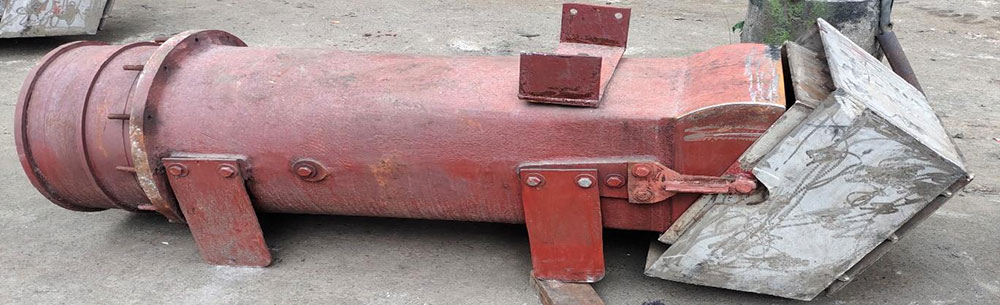
- The flue-gas exit temperature is linked with the boiler design rather than the combustor.
- Accurate control of the amount of air is essential to boiler efficiency:
- Too much air will cool the furnace and carry away proper heat.
- Too little air and combustion will be incomplete, unburned fuel will be carried over, and smoke may be produced.
Trash Plates
The trash plate is one of the most critical components of a sugar mill. It is placed in the middle of the three crushing rolls and is adjusted to obtain maximum juice extraction from the canes, increasing efficiency. The trash plate is subjected to abrasive wear combined with corrosive wear from cane fibres and extraneous sand particles and hence to be protected against wear.
Roller Shaft Journal
The Rollers in a sugar mill are given a drive-by to rotate and crush the canes. Due to continuous operations, the journal area of the roller shaft gets worn out, which affects the drive. The journal gets worn out due to frictional as well as corrosive wear. Being an essential component of a sugar mill, it needs to be ensured that the journal is in good condition during the entire crushing season.
Hammers
Hammers used in sugar mills crush the cane to extract juices. They are critical components, and a minimum of one season life is required to ensure productivity. Hammers are subjected to impact, abrasion, and corrosive wear.
Headstock
Headstock in a sugar mill is subjected to corrosive conditions due to juices extracted from sugar cane. This leads to wearing out of the headstock, and it needs to be protected from corrosion.
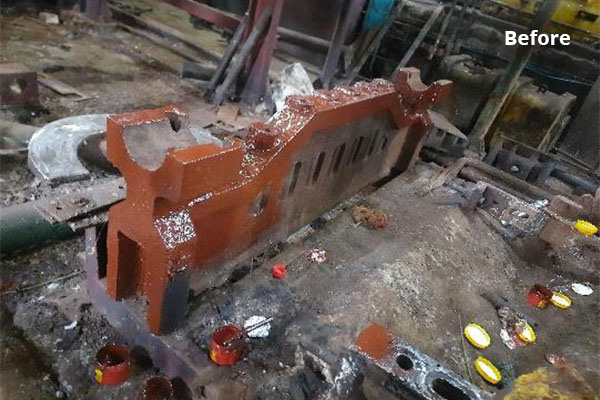
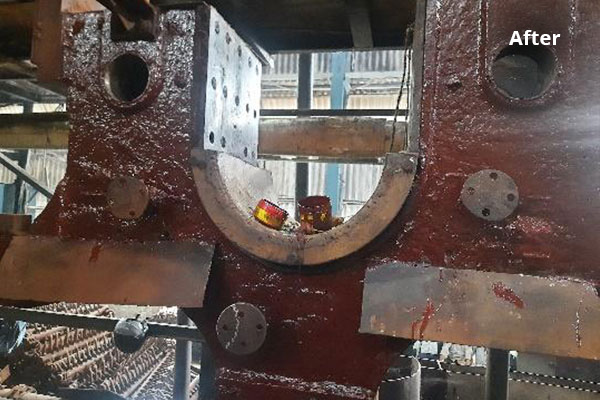
Bull gears used in the sugar mill are critical components to run the rollers and are subjected to heavy load. A crack in bull gear may lead to high downtime for a sugar mill, especially during the crushing season.
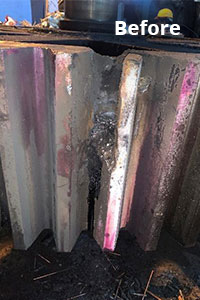
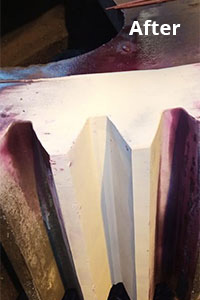
Excavator
Excavator is the equipment used to dig, move and handle earth on a large scale. It is extensively
used in the mining industry. The excavator is heavy construction equipment consisting of a boom, stick, bucket and cab on a rotating platform (known as the “house”). The house sits atop an undercarriage with tracks or wheels.
Components (Base Metal) | Problems/ Applications | Cause |
---|---|---|
Bucket (MS/Mn Steel) | Wear on Surfaces | Impact and Abrasion |
Bucket (MS/Mn Steel) | Crack | Thinned out due to improper handling |
Tooth Point (Mn Steel) | Joining | Break due to Impact |
Boom & Stick (Steel) | Cracks | Thinning due to Improper handling |
Pin Area (Steel) | Cracks | Improper handling and loading |
Hammer Cylinder
Components (Base Metal) | Problems/ Applications | Cause |
---|---|---|
Hydraulic Hammer (Steel) | Cracks | Due to excessive vibrations |
Ripper
Components (Base Metal) | Problems/ Applications | Cause |
---|---|---|
Teeth | Wear | Due to abrasion and Impact |
Shovel
Components (Base Metal) | Problems/ Applications | Cause |
---|---|---|
Under Carriage Components | Cracks and Wear | Wear due to improper surfaces |
Grouser Shoe | Crack | Uneven Surface |
Dozer
Components (Base Metal) | Problems/ Applications | Cause |
---|---|---|
Track Roller | Wear | Abrasion & Impact |
Idler | Wear | Abrasion |
Sprocket | Wear | Abrasion & Misalignment |
Chain Links | Wear | Abrasion |
Cutting Edge | Wear | Shearing Action |
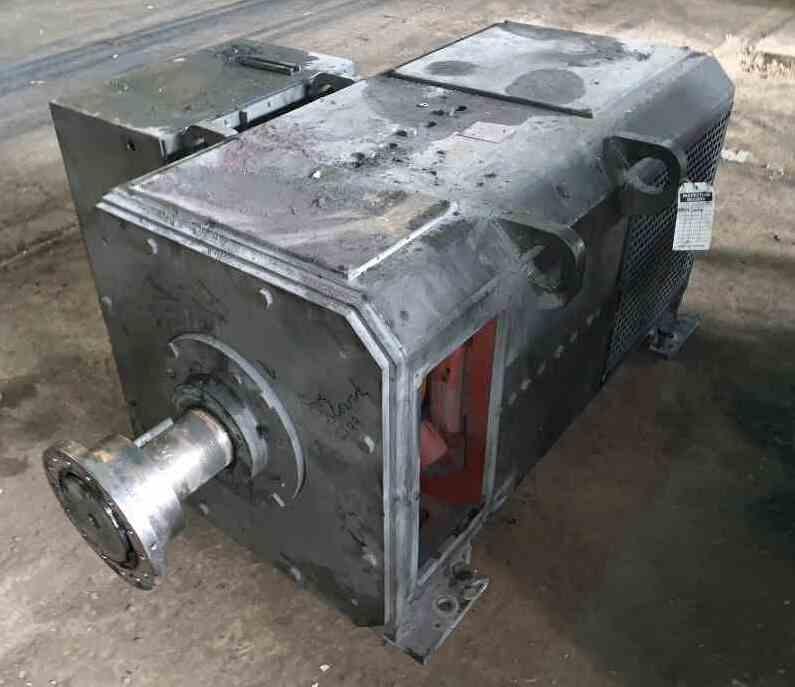
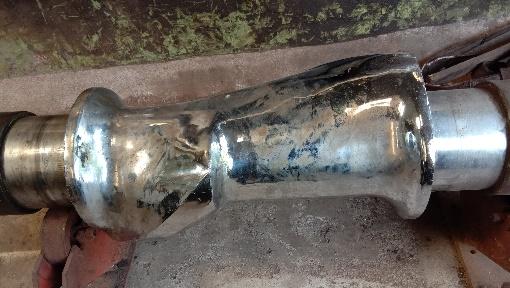
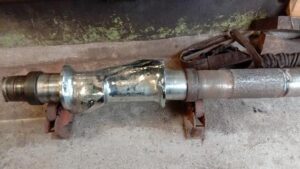
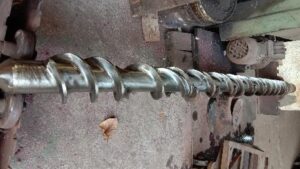
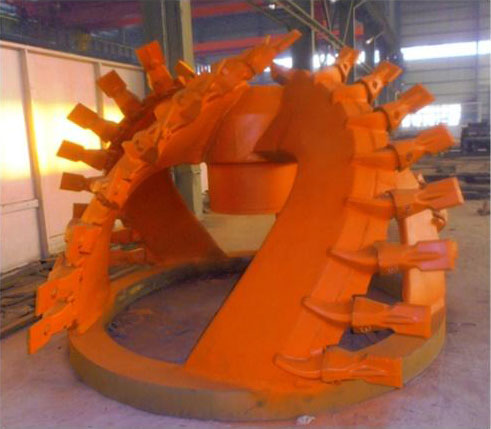
Component Details Component : Dragging Cutter Teeth. Wear Tear : Abrasion and Erosion. Down Time Loss : Cargo Ship Traffic and their waiting time. Base Metal : Mn Steel/ Cast Steel.
EWAC Solution : We have the best product range for the build-up and base layer with hardening properties, which provides the best cushioning for the hard facing layer. We have numerous products for hard facing, which we can select according to their application environment, such as the presence of soft soil, rocks etc.
Savings :
- Customers break downtime reduces so they need not change the cutter very frequently.
- Cargo ships being held due to soil and rocks hurdles is reduced.
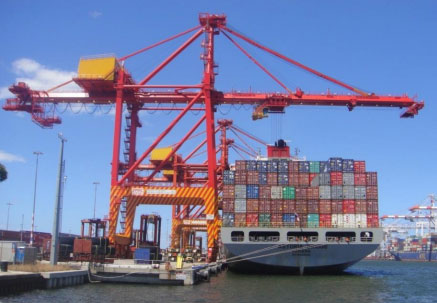
EWAC Reclamation Facility (ERF)
EWAC Reclamation Facility (ERF) specializes in critical turnkey reclamation jobs involving weld surfacing, machining, pre & post weld heat treatment with the latest technologies and up-to-date surfacing materials.
Why We Stand Out
- A breakdown results in functional stoppages and monetary losses in any industry. Our Services team support with on-site guidance is available 24/7
- Thanks to our widespread network of Weld-Technicians and Application Engineers stationed at more than 120 industry-specific locations in India, we have created new benchmarks for ‘Minimum Mobilisation Time’ to attend to any breakdown call of a customer.
We believe in the adage – ‘A minute saved is a penny earned.’ Over the years, the EWAC Services team has demonstrated technical expertise & repeated reliability and earned Customer Trust in offering turnkey solutions for jobs such as:
- Kiln Tyre Crack for Cement
- Boiler Tube Coating for Power
- On-site spikes crusher touch-up hard facing in Steel manufacturing
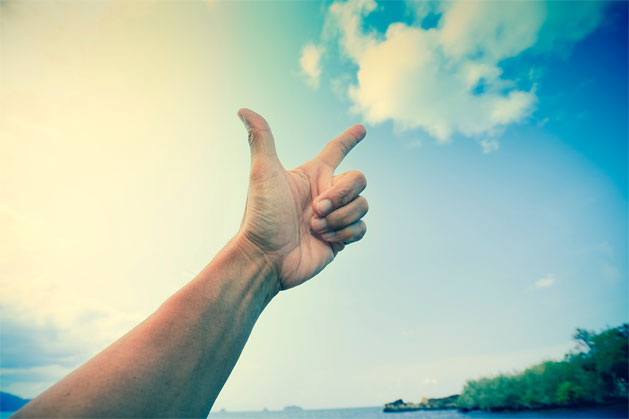
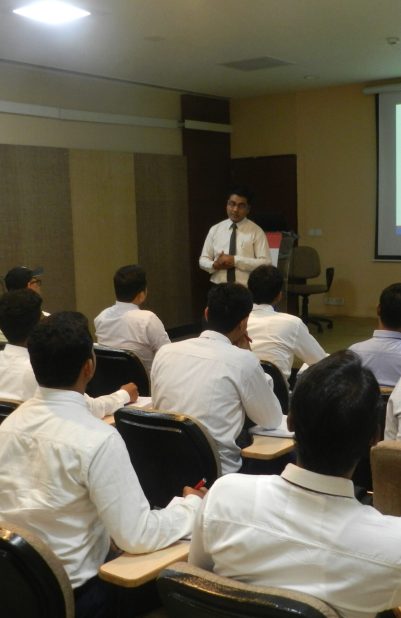
Team details & Workshop locations
Tools Tackles & Safety
Safety is always the greatest priority for us. Our team at workshop as well as at customer’s place, are always adorned with all necessary safety gears. Before starting of any job, Tool box talk & risk assessment is the first action.
For specific jobs, a toolkit is specially designed that includes complete set of tools & tackles, all necessary safety PPEs and sturdy power sources. This ensures zero interruption to continued service support. All equipment are shipped in dedicated containers to almost all work locations. Our service engineers are well equipped to take up even the electrical breakdowns.
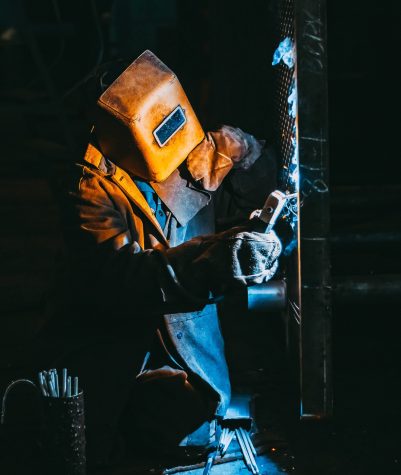