Steel
Steel Industry plays a predominant role in providing the desired momentum to a nation’s economy. Over the years, the radical developments in different industrial and economic policies added relevance to the sector.
The major thrust areas that need the focus are as follows :
- Reduction in downtime
- Optimizing consumption of spares
- Lowering inventory carrying cost
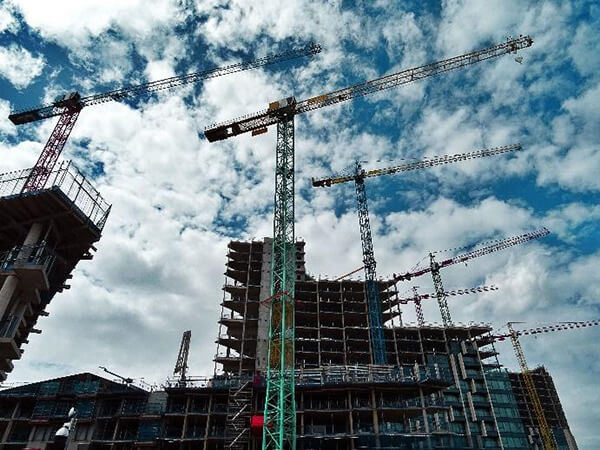
To achieve the above aspects, we have constantly endeavoured to supplement the various efforts being taken by the Steel industry.
The scientific approach to wear analysis and the versatile range of products and processes developed by EWAC R&D, together with the technical expertise of engineers, eventually aid the Steel Industry in achieving its maintenance goals seamlessly.
Applications
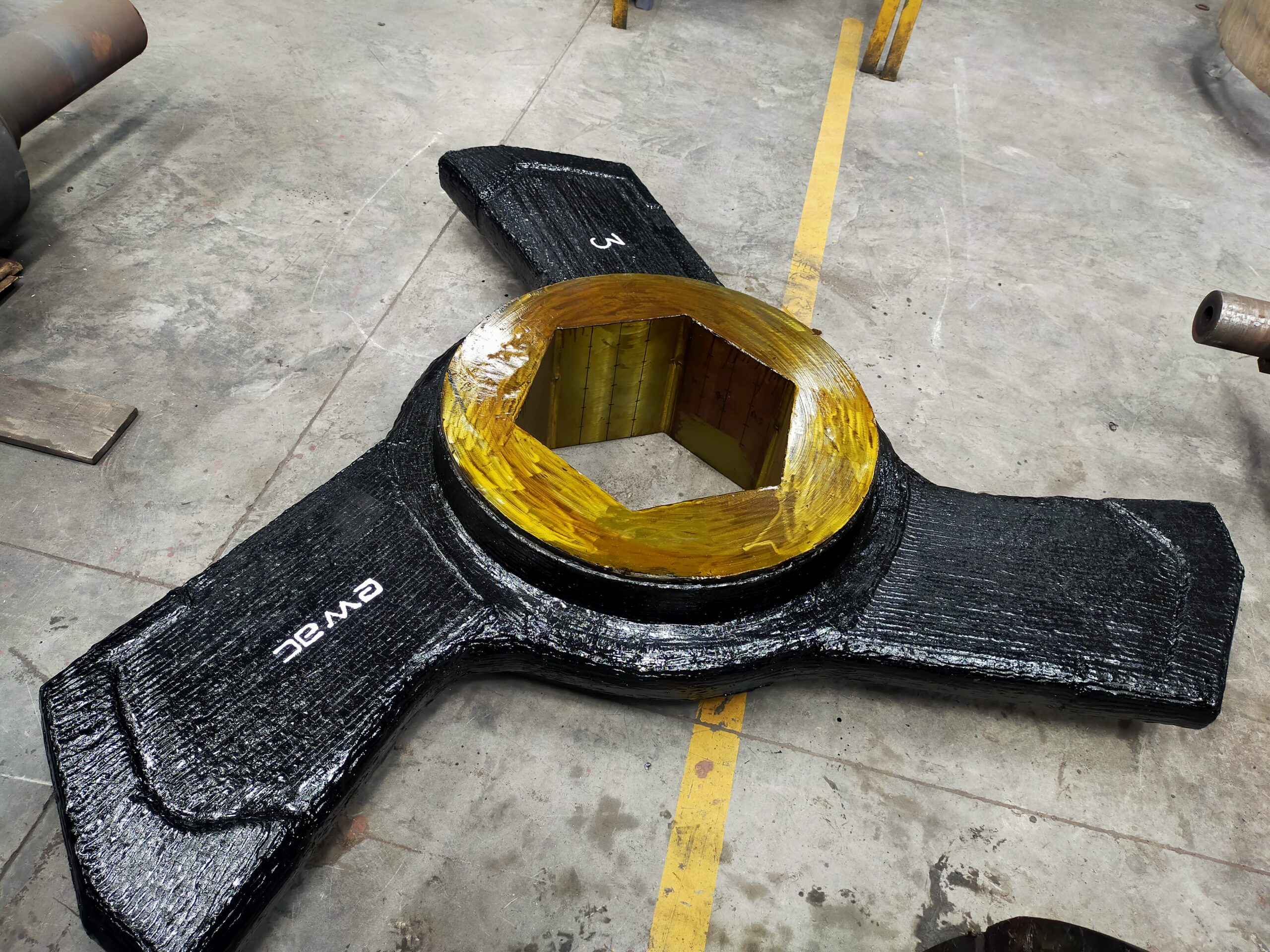
In an integrated steel plant big boulders of various minerals like coal, limestone and dolomite are crushed into smaller lumps of uniform size for use, with various types of hammers.
So, we see various hammer mills using hammers of different base materials, shapes and sizes engaged in crushing the above raw materials.
The hammers are subjected to severe impact and abrasion which are replaced at frequent intervals as consumables. EWAC Alloys with its six decades of experience in reclamation technology has developed high performance ready to use crusher hammers for coal and flux. We are a leading supplier of these hammers, are established in many integrated steel plants for their life-prolonging factor, high crushing efficiency, reduced downtime and overall techno economics.
Steel Mill rolls support solidified billets, slabs with a surface temperature above 500°C to avoid the bulging of the slab/billet due to the Ferro-static pressure of solid metal. The cooling water that flows continuously generates surface stresses and initiate thermal cracking. In addition, slab/billet skin is covered by mould’s flux which reacts with water and generates a highly acidic and corrosive environment and ultimately deteriorates the surface of the roll.
How EWAC Alloys Can be Helpful:
- With 60 years of experience and research, we have innovated specialized welding alloys to further clad these raw forged rolls with thermodynamically controlled microstructure.
- This further enhances performance with clean and carbide-free grain boundaries and uniform dissolution of corrosion inhibitors in the microstructure.
- Highly adherent sub-micron film formation on the roll surface provides excellent resistance against oxidation and corrosion.
- Cladding on rolls increases resistance to thermal softening, thermal cycling, and metal to metal wear and almost doubles the life of rolls compared to raw uncladded forged rolls.
IMPORTANCE – Vital
LEAD TIME – 90 Days
Wear and Tear Detail
In simple forged rolls, the rate of wear is high as after erosion of the top surface layer, further wear is aggravated ultimately leading to a threshold limit beyond a usable point.Loss due to unavailability/ Down Time
The application of rolls is in CCM which is directly related to production. Failures & frequent wear leads to loss of productivity and losses.
Saving
Doubling the life of rolls at an additional cost of 25% of forged rolls value leads to a big time-saving. Further, after wearing of cladded surface, the rolls barrel can be re-cladded thus salvaging out the life from erstwhile to be scrapped rolls.
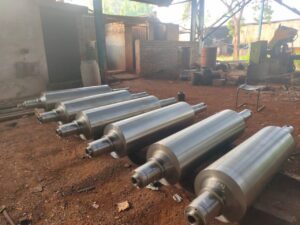
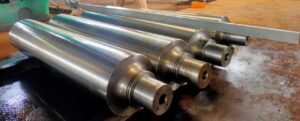
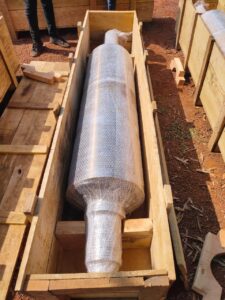
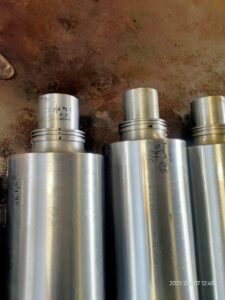